When selecting painted panel facades, there are numerous considerations with long-lasting good looks scoring highly with asset owners and architects. However, the road to achieving this is not as straightforward as it initially appears. Is marine grade aluminium the shining pinnacle of the facade industry, or false hope?
As with all things in the building and construction industry, materials need to be evaluated based on their performance within the intended usage situation before being deemed ‘Fit for Purpose’.
Aluminium is no different, it has been the material of choice within the facade industry for many years, but the industry’s perception that ‘Marine Grade’ aluminium must deliver superior performance when used on painted aluminium panels, needs to be reviewed.
Underpinning aluminium’s resistance to the detrimental effects of corrosion is its ability to form its own protective oxide barrier. The oxide barrier is a regenerative, passive layer that protects the base metal from progressive corrosion. This core ability of aluminium to resist corrosion does vary between different grades; however, both the 3003 (widely used in architectural facades), and the 5052 (marine) grades, are some of the best-in-class examples when it comes to corrosion resistance.
In heavy marine applications, where continuous exposure to the damaging effects of salt water is experienced, uncoated 5052 marine grade aluminium, in its raw form, will outperform the more conventional 3003 grade – it’s a fact.
But for the purpose of architectural facades, where aluminium is coated, bent to shape and installed as curtain walls on buildings, the benefits of 5052 aluminium may be less obvious.
To challenge this thinking, a 1,000-hour Neutral Salt Spray Test was commissioned in accordance with AS 2331.3.1 and both 3003 and 5052 grades were tested to determine which material came closest to satisfying the ‘Fit for Purpose’ status within painted architectural panels.
The test was carried out independently by Robert Jeffrey at Pacific Testing.
Two panels were prepared from roll coated aluminium, grooved and fabricated into a standard cassette format.
The surface of each panel was deliberately scratched down to bare metal, and the resulting reaction to the environment was observed and documented.
- Sample A: 3003 grade aluminium with primer and single coat of PVDF
- Sample B: 5052 grade (marine) aluminium with primer and single coat of PVDF
Findings
1. After 1,000 hours, Sample A recorded some oxide streaking and low-level blistering across the panel face and on fringes emanating from the scratched areas. Sample B produced similar results with some low-level blistering occurring on the panel.
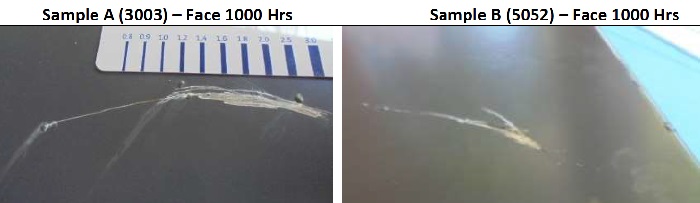
2. Across the cassette bend, in areas affected by fabrication, Sample A recorded low levels of blistering, while we saw high-level blistering being recorded on Sample B in several areas across the bend.
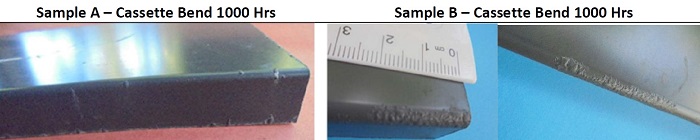
3. Reviewing the cut edges, mild oxidisation can be seen in Sample A along with low-level blistering where water has migrated under the cut paint edges. Sample B has some signs of discolouration on the bare cuts, with no blistering recorded.
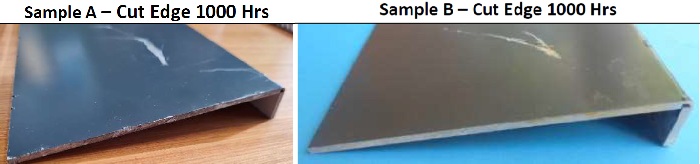
Analysis
Based on the test results, 5052 Marine fails to deliver a performance advantage over the widely accepted 3003 grade. Furthermore, on sections where the substrate was mechanically fabricated (routed and bent), 3003 significantly outperformed the 5052.
If we use this test to predicate real-life performance outcomes on architectural facade applications, grade 3003 would have to be deemed as a better ‘Fit for Purpose’ base material.
We can conclude that while low level of unsightly blistering can occur on cut edges, these are concealed by caulking/sealed joints, and largely invisible. The cassette bends are, however, highly visible, and any corrosion seen here will destroy the overall look of the facade.
Why is 5052 blistering across fabricated areas?
The blistering we see is a direct result of poultice corrosion, which occurs when aluminium is exposed to trapped water in the absence of circulating oxygen. This can only happen if moisture finds a pathway under the protective PVDF coating surface.
What is the likely cause?
Under normal circumstances, it’s the coating that provides weather protection, and forms the first line of defence. When the coating is compromised, we revert to the formation of an oxide layer to protect the aluminium from further degradation. But it’s the formation of the oxide layer itself that compromises the facade appearance, breaking the coating bond and forming a surface bubble. Within the oxygen deprived bubble, poultice corrosion takes hold and proliferates, while the protective oxide layer is unable to form in the absence of oxygen.
It has been widely documented that relative to the more flexible (workable) 3003 grade, the 5052 is prone to micro cracking when bent beyond 90 degrees. Surface cracking in aluminium can break the bond between the coating and the substrate, while allowing moisture to penetrate.
Conclusion
It is the coating and material workability properties of 3003 that make it best suited for use in architectural facades. Fabricated panels of coated 5052 have a higher likelihood of being adversely affected by bubbling caused by micro cracking and poultice corrosion.
Please note: This is an internal review - FV sourced both 3003 and 5052 samples used in the tests