The materials you choose for external cladding have a significant impact on the longevity and maintenance of your building. The use of efficient facade materials plays a critical role in optimising operational energy requirements and serving various functional qualities desired in modern buildings. External cladding not only protects the building from weather elements, but also provides noise control and thermal insulation, and adds visual appeal, making it a key component of any facade.
Cladding choices are many – over the years, there has been an increase in the types of materials used for cladding applications with options ranging from aluminium, glass, timber and brick to fibre cement, autoclaved aerated concrete (ACC) and steel. Architects and designers need to give sufficient weight to the process of evaluating cladding materials that are fit-for-purpose.
“The material choice depends on the purpose of the cladding, the environmental conditions of the site, the material’s architectural properties and project limitations,” says John Lorente, executive general manager – construction, Big River Group.
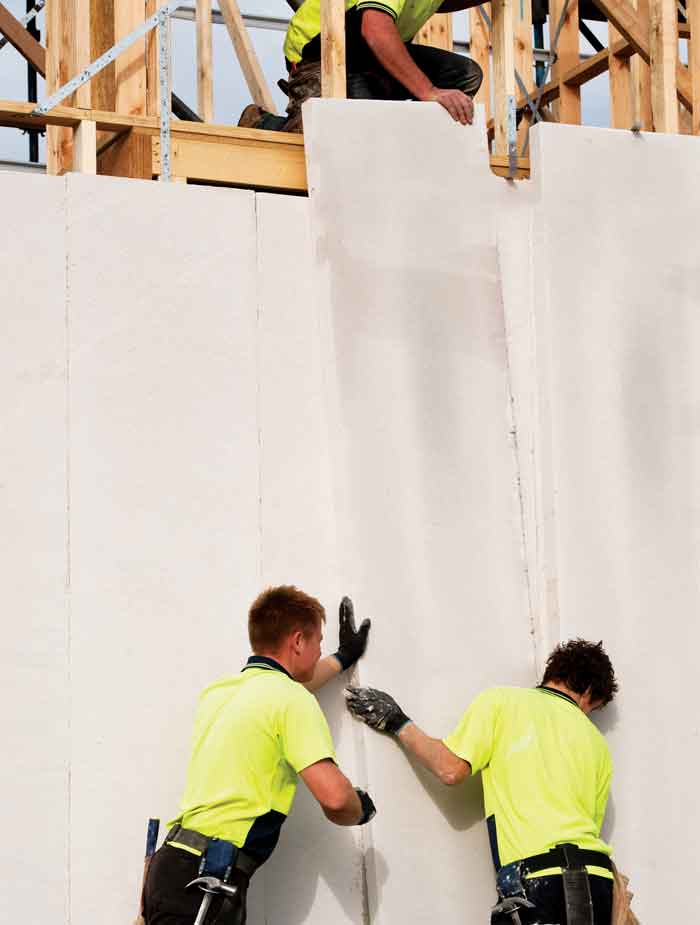
Two of the most commonly used materials in residential construction are brick and ACC due to their exceptional architectural properties, longevity and ease of manufacturing. While both are designed to perform as external cladding products and have many common features, each material offers unique advantages for residential construction.
Big River Group has released a new and informative guide for specifiers, identifying the differentiating factors of both brick and ACC for cladding applications.
Autoclaved aerated concrete
Invented in the 1920s, ACC is a lightweight concrete product that has been manufactured to contain closed air pockets.
“Due to the material’s closed aerated structure, ACC panels are highly effective insulators, which help reduce a building’s air-conditioning load in comparison to conventional construction. AAC has up to four times greater thermal resistance than standard house bricks. When incorporated into an energy-efficient design, this superior thermal performance reduces the amount of energy required to heat or cool the building, resulting in significant cost savings for homeowners,” says Lorente.
Benefits of building with ACC:
- Acoustic insulation: Closed air pockets result in superior soundproofing and acoustic insulation properties.
- Fire resistance: A porous structure gives superior fire resistance. It is also inorganic, incombustible and does not explode, so it is well suited for fire-rated applications.
- Good strength and durability: One-fifth the density of normal concrete, AAC offers half the bearing strength and can be safely used to erect structures up to three storeys high.
- Speed of construction and reduced costs: Lightweight and easier to handle onsite with standard construction tools; ACC panels are also produced to the exact sizes needed.
- Environmental benefits: Comprised of 80% air, AAC contains far less raw materials than standard concrete.
- Modern aesthetics: AAC panels are suited to a wide range of modern architectural styles, with rendered finishes that can create distinctive visual effects and contemporary aesthetics.
All the benefits of building with ACC can be found in Big River Group’s MaxiWall, a strong yet lightweight walling panel made from AAC and reinforced with corrosion-protected steel mesh. Designed for buildings built with standard timber or steel framing, MaxiWall’s combination of excellent thermal performance, acoustic insulation, and fire resistance, offers an ideal option for all types of residential projects, from detached dwellings to multi-residential housing. Its contemporary rendered finish offers a more stylish and sustainable alternative to traditional brick and concrete and its lightweight handling contributes to faster, more efficient installation, saving on costs, time and energy.
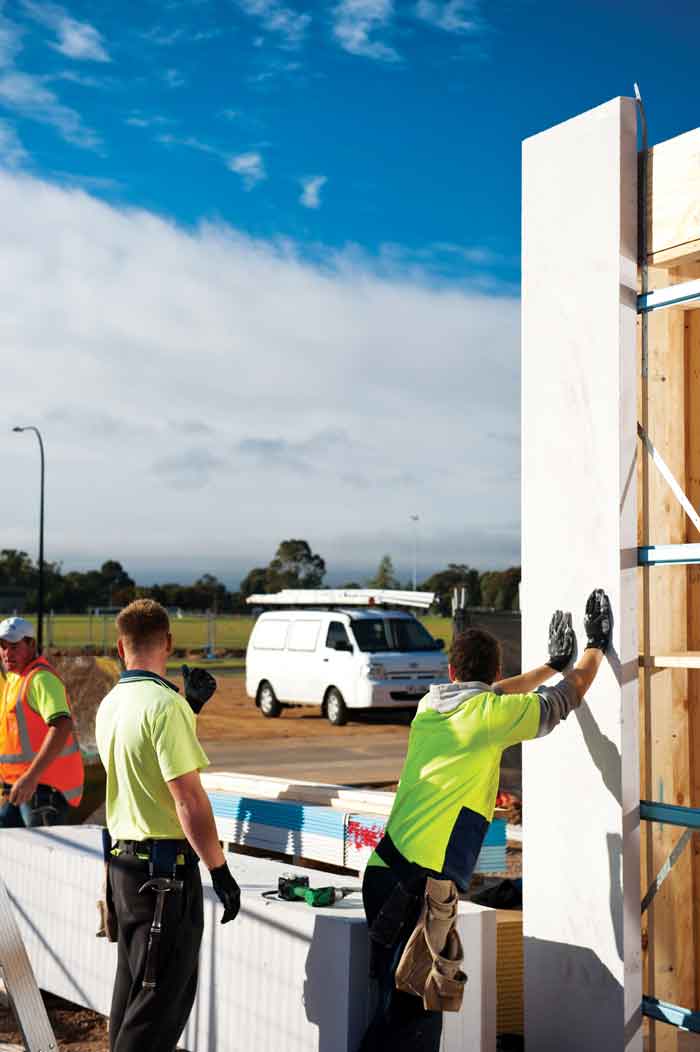
“Installing one panel of MaxiWall is equivalent to installing about 75 bricks, that creates a huge saving for builders and homeowners on site in relation to cost,” says Lorente. “Labour costs are reduced and so too is material wastage on site.”
Bricks
Bricks are among the most commonly used materials for residential construction due to their high strength, excellent fire resistance, durability and aesthetic versatility.
Benefits of building with bricks
- Buildability and availability: Clay and concrete bricks are manufactured throughout Australia and readily available at competitive prices.
- Durability: Bricks offer high levels of durability and element resistance as they are also non-combustible, even after many decades they remain strong, reliable and relatively maintenance free.
- Moisture resistance: Clay brickwork is not completely waterproof, but it does effectively resist the penetration of rainwater with the appropriate detailing.
- Low maintenance: Due to its strength and durability, some types of brick require little or no maintenance.
- Thermal mass: Brick has exceptional ‘thermal mass’ properties, which refers to the ability of a material to absorb, store and release heat.
- Classic appearance: The classic style of brick construction is warm and inviting with a selection of earthy hues and textures.
While both ACC and brick are undoubtedly strong options to consider for a construction project and designed to perform as external cladding products, each material offers unique advantages for residential construction. AAC offers the added benefits of cost and time savings and sustainability. Ultimately, the decision to use either AAC or brick will depend on the specific requirements of the project, including the desired aesthetic.
Download the whitepaper here.