“Innovation distinguishes between a leader and a follower.” Steve Jobs, Apple founder.
This last column before the federal election concentrates on innovation and manufacturing; two design initiatives at the heart of the Labor campaign that have received very little attention.
I want to illustrate their importance through two buildings for the very progressive company Kingspan, a story of innovation and initiative (and some stupidity, for which you’ll have to wait to the end).
Reflective insulation
For a long time, we took our cues on sustainable building design from Europe and North America where bulk insulation controls heat transfer by conduction and convection. But in Australia's harsh summer sun reflective insulation is crucial in reducing radiant heat in roofs and walls - which most students miss unless you were taught by a quality building physicist like Alan Coldicutt, Jack Greenland or Steve King.
Hence my admiration for the Australian invention of AirCell by Brian Tikey in WA in 1998 – improving on the traditional aluminum foil insulation with a form of reflective ‘bubble wrap’ so that it had both convective and radiant properties. The orange surface that reduces glare during installation is an organic layer that disappears over time to reveal the shiny surface underneath.
Through sustainable discussions I met Scott Gibson, Air-Cell MD, almost 20 years ago, just as it was developing a thin ‘blanket insulation’ that could assist as a ‘thermal break’ in the increasing use of steel framing to replace (less-sustainable) timber framing. Called ‘Insulbreak’ it was part of the success saw it taken over by Kingspan Insulation, one of the big claws of the then ‘Irish Tiger’.
Kingspan HQ 1
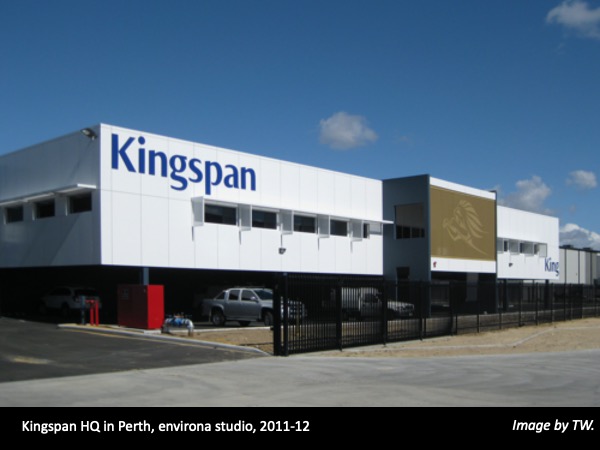
In 2011 Kingspan commissioned a new office and warehouse facility in the Perth industrial estate of Malaga and Scott Gibson asked us for a design. The site was uninspiring: flat, treeless, facing to the west with high voltage power lines. Together with Gibson we designed a ‘big box’ with a modest office building in front; highly insulated (as you would expect) with reduced, well-shaded, glazing; LED up-lighting, and a featuring a folded AC duct made of Kingspan insulation.
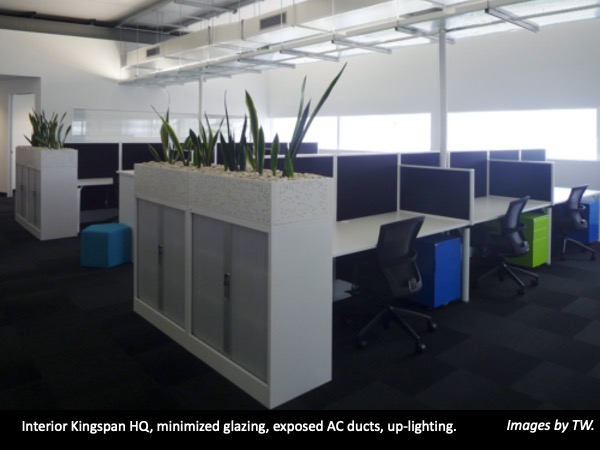
It was so well received by the staff that Gibson reported that, not only did it make energy and water savings but critically, effective staff working hours went up and absenteeism and churn went down. All the hallmarks of a ‘real green’ building.
Kingspan HQ 2
Soon Kingspan wanted to build a local factory to make their ‘phenolic resin’ insulation, a solid board insulation that can be bonded to other materials such as fibro cement or plaster board. The advanced manufacturing process developed by Kingspan was the best in the world; and at that time there were only two other facilities. A bold move by the company to manufacture in Australia to serve the Asian market, rather than the other way round.
When Scott Gibson asked for advice, I suggested that a project of this complexity and scale should be handled by a large entrepreneurial design firm, such as Jacobs, where my good friend Clinton Murray had just started as chief architect. They laid out a masterplan and assisted in securing a site in the area being redeveloped around the closed Ford Motor factory. The sites in Somerton on the outskirts of Melbourne had formerly manufactured tyres, batteries, wiring harnesses, and so on, all of which closed when Ford did.

This was in part prompted by the possibility of funding through the Melbourne North Innovation and Investment Fund, or NMIIF, a $25 million fund established in August 2013 by the Rudd Labor government ($15m) and Dennis Napthine’s Victorian Liberals ($4.5m) and Ford Australia ($5m), for projects that would generate substantial new jobs in the Melbourne north region. Kingspan was awarded $3m towards their manufacturing plant.
Once approval of the Jacobs scheme was negotiated through the various layers of government, more collaboration was needed. Construction at this scale can be difficult, and Kingspan engaged local Melbourne firm Corplex, well-versed in factories, to manage the construction and leasing of the offices / factory / warehouse facility. Corplex hired their usual architects (Watson Young) to detail up the construction documentation.
Going green
Given that the product to be made, insulation, is at the center of building sustainability, Gibson was insisting on a ‘five-star Greenstar’ building. We were bought on board to advise on sustainability aspects and update the design ideas and detailing from the building in Perth. To their credit Corplex engaged a Greenstar accredited professional in-house to help their processes.

The factory required a long linear line, the warehouse a big box and the small office building faced south (so a different glazing regime to Perth), all surrounded by a huge apron allowing trucks to deliver (somewhat volatile) materials and collect the product for distribution. The roof is vast, good for PVs and water collection, and the innovative Kingspan automatic skylights.

Wrangling the meetings and discussions for a building of this size is not easy. This is the hidden part of the architectural process, rarely discussed, but at the center of most of our working lives. And that’s before the sustainability creativity desired.
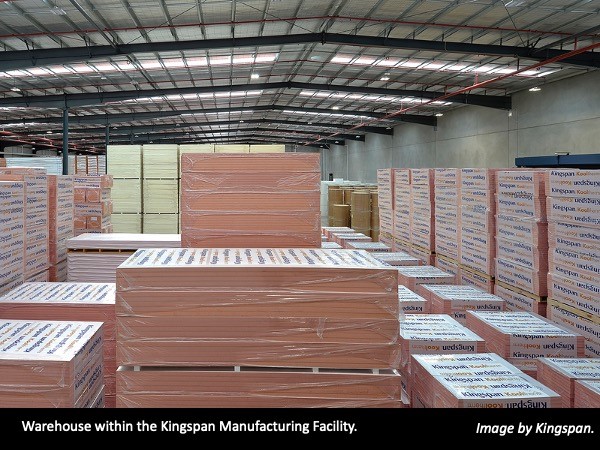
Whilst Kingspan has its triple bottom line, if the building is not profitable then the two-legged stool will collapse. The Greenstar process is difficult enough for typical buildings such as offices, even more complex and opaque for a factory / warehouse. Despite our best efforts, accreditation for design and construction never eventuated, but still Gibson saw the building is being both energy and cash positive, as he tells A+D here.

The care taken in its design and construction is eventually vindicated: after two years of assessment the performance level of the building is awarded ‘Six Star Greenstar’, the first factory / warehouse to achieve that top level. An innovative company, employing upwards of a hundred people, manufacturing selling and distributing an innovative material, in an innovative building.
Oh dear
But there’s a downside, highlighted by Josh Frydenberg, then environment minister, when asked to open the building. I was asked to show him and his amanuensis around. I've met many politicians during my time in Canberra and serving on government boards, but I've never met anybody so dull and uninterested in innovation. But wait, it gets stupider.

At a Q+A session Frydenberg was asked if the federal government could offer some assistance in enforcing quality and safety regulations for manufactured materials (given there were little to no safeguards on inferior importations). He had just seen the factory and had the importance of Codemark explained. Frydenberg's reply was “As a Liberal, I’m always in favor of less regulation, not more”. A hundred pairs of shoulders slump.
That failure to understand the importance of regulation of standards continues. In Senate estimates last year Senator Rex Patrick denigrated Kingspan's products by asking questions that were seemingly based on one of its overseas made competitors. Kingspan expends ever more of its energies in combating this misinformation.
The only consolation is that in a week's time, it is possible that neither Frydenberg nor Patrick will have a job in our federal parliament. And Anthony Albonese, and his Minister for Industry and Innovation, Ed Husic, will embark on reviving Australian manufacturing.
Tone Wheeler is principal architect at Environa Studio, Adjunct Professor at UNSW and is President of the Australian Architecture Association. The views expressed here are solely those of the author and are not held or endorsed by A+D, the AAA or UNSW. Tone does not read Instagram, Facebook, Twitter or Linked In. Sanity is preserved by reading and replying only to comments addressed to [email protected]