The building industry is starting to realise the benefits of engineered or precast brick panel systems, especially in terms of speed and ease of construction. Danielle Bowling spoke to two firms who’ve seen the benefits of such systems in recent projects.
Marc Burmeister architectural representative – commercial facades at Robertson Facade Systems
During the last 10 years, the notion of pre-assembling has been developing to a point where concrete panels are replacing other framing/sub-strate materials. This development is improving our methods of construction; a constant consideration in the building community.
One of the most significant concrete innovations has been Robertson’s Brick Inlay System. A process that removes the labour intensive brick laying task from the site and gives it to a concrete contractor. The system features brick shape tiles that are laid in the concrete form bed before any concrete is poured. The next step involves placing reinforced concrete in this form, over the top of a ‘blanket’ of brick tiles that have been secured in place, ready for the concrete to be poured on them.
Robertson’s Brick Tile, used in the Inlay Systems, displaces concrete and does not add to the depth of these panels. These clay tiles have a porosity which makes the bond, created during the curing process, strong and durable. In fact, our tiles are fired at such high temperatures, that we expect the clay to outlast the concrete, ultimately assisting to preserve the integrity of the core panel material.
The authenticity of these pre-made walls comes from two key areas: material and detail. The clay tile is the same material as a contemporary brick, featuring the long life attributes that you expect from hand laid brick work. Our brick inlay systems also features corners and ledges enabling designers to incorporate genuine ‘depth’ when they reach corner sections and panel ends, contributing to the illusion that genuine brick work has been laid.
In addition, the brick tile allows architects to create angles and details that could not be done had they chosen to use a 110mm thick brick. This tile can be cut and joined at unusual angles to mirror the concrete form and follow radius sections in the same way as a brick can be managed.
Like brickwork, a 10mm gap (or perp) separates each brick tile in the panel. This 10mm wide concrete is shaped to look like a raked mortar joint and appears as though a tradesperson has taken the tip of his trowel and struck it under the brick tile. As we are working on a flat surface in the concrete contractors yard, any bond pattern or direction can be utilised. This means that architects can create brick facades that could not have been built in the traditional manner.
Today, the Robertson’s brick inlay system is used extensively by apartment, school and shopping centre builders because it reduces risk by taking key building elements off site, whilst dramatically improving the speed of construction.
Santorini Apartments, ST KILDA Victoria
-
Architect: Design Consortia Australia
-
Builder: Hansen Yuncken
-
Concrete Precaster: Victoria Precast
-
Tile Specification: Australian Standard, Terracotta/Plum & Blue/Black blend
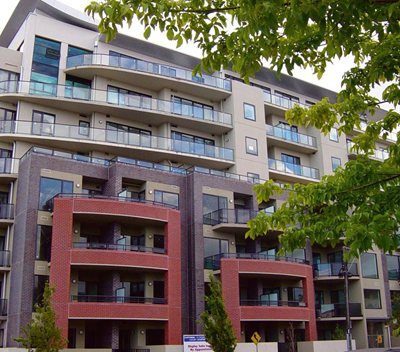
Curved brick walls require care and attention to detail to ensure each balcony faithfully matches the next. The solution on this project was to create a form bed that curved and supply these key brick facade elements as pre-manufactured sections.
This site is along a major traffic artery and managing the construction on such a busy road could only be handled by utilising the time and energy savings you get from using concrete precast. This meant the builder could focus more time on interiors and get the rooms in shape quicker than had conventional bricks been laid.
St Josephs College, Ferntree Gully, Victoria
-
Architect: Bellemo & Catt Architects
-
Builder: S J Higgins
-
Concrete Precaster: Melbourne Precast
-
Tile Specification: Australian Standard, Yellow Glaze & Rustic Tan
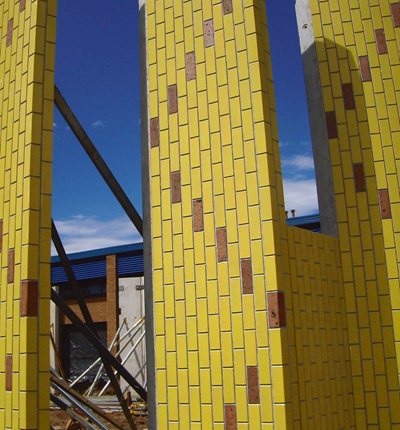
The Snap brick inlay system for precast concrete allowed the designer to create a reception building for this school, utilising load bearing panels, which overcame the issues associated with turning stack bond brick patterns on their side.
The off-site manufacturing of the intricate panels featuring unique angles, combined with the quick and easy characteristics of precast assembly, meant the project proceeded with a minimum of fuss, despite working in close proximity to a number of students and working with glazed materials that are quite precious.
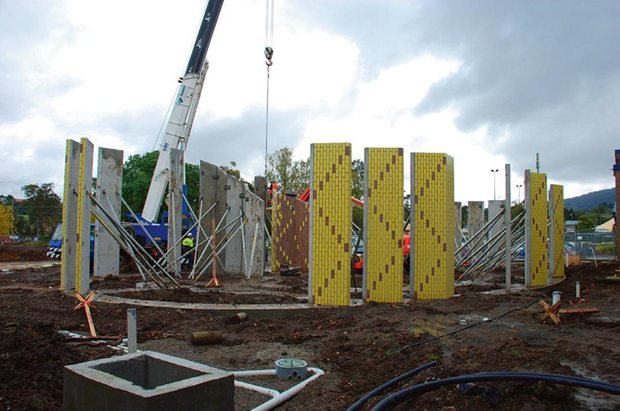