THE NEW ROYAL CHILDREN'S HOSPITAL, PARKVILLE
Billard Leece Partnership and Bates Smart Architects (BLBS)
The brief was to deliver a $1 billion hospital campus and provided an opportunity to deliver new Models of Care incorporating innovative international healthcare concepts including: evidence based design principles family centred design approach environmentally sustainable design introduction of daylight and nature into work and health care settings co-location of clinical, research and education facilities
The new Royal Children’s Hospital (RCH) project was delivered as a public private partnership (PPP) under the State Government's Partnerships Victoria model.
The Children's Health Partnership was the consortium responsible for financing, designing, constructing and maintaining the new hospital building. The consortium consists of International Public Partnerships as equity holders, Lend Lease as builder, Spotless Group as facilities manager and architects Billard Leece, Bates Smart and HKS (US).
The client’s tender documentation set the project’s sustainability criteria at levels never achieved by any previous healthcare project in Australia. We delivered the ‘greenest’ hospital in Australia, based on the pilot rating tool that was in place at the time. A key challenge was that the project design commenced prior to the release by GBCA of the greenstar healthcare v1 pilot, rating tool. Hospitals are complex and diverse projects to assess. A significant amount of built in equipment is not ‘green star’ rated, for example mattresses and specialist medical equipment. It is also challenging to apply modelling methods for calculating thermal comfort in terms of predicted mean vote (PMV) in patient areas. Hospital operations are also difficult to assess or benchmark, for example the use of a black water treatment plant has to exclude certain contaminated waste.
The brief called for stringent minimum daylight targets. A ‘street’ runs through the middle and points due north ensuring that the street is light filled throughout the day. Gardens wrap around the entire footprint of the hospital.. Each block of the hospital thus faces directly into parkland. The 7 storey development fits comfortably within the parkland setting and within the tree canopy height that surrounds it. The buildings are also designed to fit into the parkland environment using the colours and textures of trees to allow for a very integrated solution. Parkland environments have been found to be the healthiest and uplifting of environments and so we sought to use this park language in the architectural language to produce a healthy architectural vocabulary.
Special attention was paid to the natural textures, forms and colours of the park and how this could directly inform the material expression of the building. The glazed coloured leaf petals blades used as sunshades on the west façade are particularly symbolic of the way the building integrates nature into the building. The design process resulted in a detailed study which indicates how the built environment infused with the experience of nature can speak to the child and help provide a therapeutic hopeful backdrop for those visiting the hospital. On some levels roof top areas were utilized as garden areas. Solar panels were introduced onto the north facing roof over the In Patient Building.
INITIATIVES
-
Rainwater collection from 75per cent of roof area with collection tanks for 85per cent run-off area
-
Blackwater treatment plant recycles selected wastewater (excludes waste water from Labs and cytotoxic-use areas) for use in toilet flushing, cooling plants and irrigation of interior gardens and Royal Park
-
Landscape irrigation system with rainwater
-
Heat recovery provided on all exhausts and mixed mode ventilation including a labyrinth applied to the ‘Central Street’.
-
Maximum levels of fly ash content in external precast
-
Armstrong World Industries floor vinyl was used throughout. Total recycled content is 31per cent. Post consumer 2per cent, post industrial 6per cent and in-process/reclaim 23per cent.
-
Maximum levels of fly ash content in external precast
-
Recognising energy as one of the most significant components of Green Building design, Lend Lease worked with the design team to develop efficient and innovative services to meet the State’s aspirations. Innovation was achieved on a number of levels across:
-
Energy Reduction through:
-
Passive design
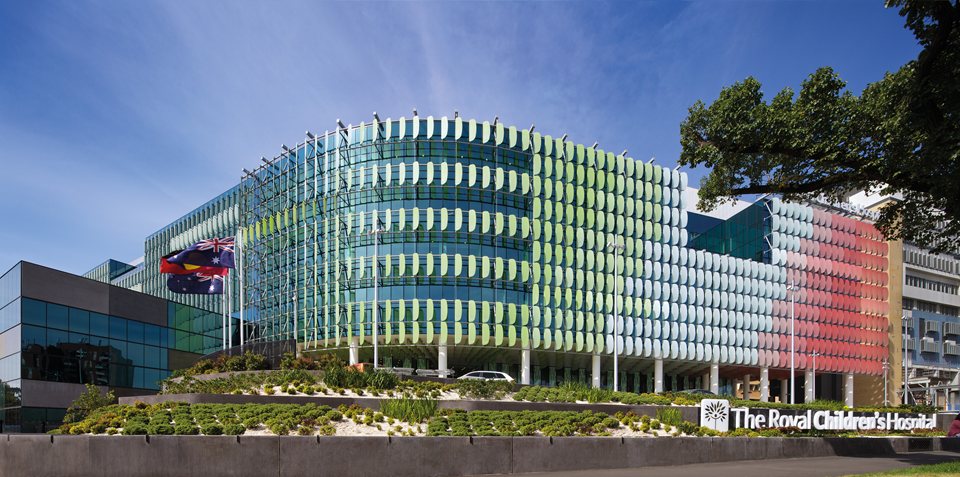
-
Solar shading
-
High performance glazing exceeding BCA requirements
-
Building insulation exceeding BCA requirements
-
Equipment efficiencies better than BCA minimum thresholds:
-
Centralised plant design for Stages 1 and 2, advantages of which include:
-
Economy of scale
-
Energy efficiency
-
Resilience
-
Low-energy lighting installations, including:
-
Use of natural daylight
-
Minimum energy efficiency specification for lighting installation
-
Electronic ballasts
-
Low-mercury content lamps
-
Maximum design luminance levels
-
Lighting control requirements, including zone switching and daylight control meteringand monitoring
-
Emission reduction and management through systems such as:
-
Carbon monoxide sensors, variable daylight and occupant-sensing controls to trigger variables peed ventilation systems
-
Car park – Zonal parking management system to reduce emissions
-
Energy reduction and reuse through system selection
-
Trigeneration systems, with significant advantages including:
-
Optimised fuel efficiency
-
Use of natural gas as fuel (clean burning)
-
Reduced maximum demand on the electricity grid
-
Reduced greenhouse gas emissions (relative to other fossil fuels)
-
Reduced whole-of-life cost
-
Use for standby generation – dematerialisation
-
2 off 1,120 kWe gas-fired cogeneration engines
-
2 off 1,260 kWr double-effect absorption chillers
-
Displace 1 off 2,000 kVA standby generator set
-
Estimated CO2 emission reduction of 9,000 tonnes per year
-
Biomass-fired boiler
-
Carbon neutral
-
1 off 600 kWth heat output
-
1 off 20 tonne storage silo for wood pellets
-
Estimated fuel delivery frequency: 2-4 times per week (4-5 tonnes)
-
Estimated CO2 emission reduction: 650 tonnes per year
-
Chilled water to tenancies (not condenser water)
-
Peak load reduction
-
Optimal usage of trigeneration plant
-
2 off 700 m³ chilled water storage tanks
-
Estimated refrigeration effect: 1,500,000 kWh per year
-
Energy and greenhouse gas targets
-
Maximum and aspirational building energy consumption
-
Maximum and aspirational GHG emissions
-
15per cent peak electrical demand reduction
-
At least 1.5per cent of building energy demand generated by renewable energy sources
-
Energy infrastructure
-
Reduce peak electrical demand of chillers by at least 15per cent-23per cent
RAVENSWOOD SCHOOL FOR GIRLS
BVN Architecture
The design of this building was initiated through a master planning process focused on creating an attractive, imaginative and stimulating learning environment that empowers students and facilitates self directed learning.
The Mabel Fidler Building is designed to be in scale with the existing school buildings and be seen as a modern insertion into a campus of varied buildings. Site accessibility due to level changes and difficulty of way finding has always been an issue for the school, along with the usability of external areas. The Mabel Fidler Building project is designed to address these issues.
Importantly, the new building provides Ravenswood with a new front door and real heart of the school. Raising the library onto the upper level created dramatic cantilevers under which are a number of different spaces protected from the elements where informal learning can take place.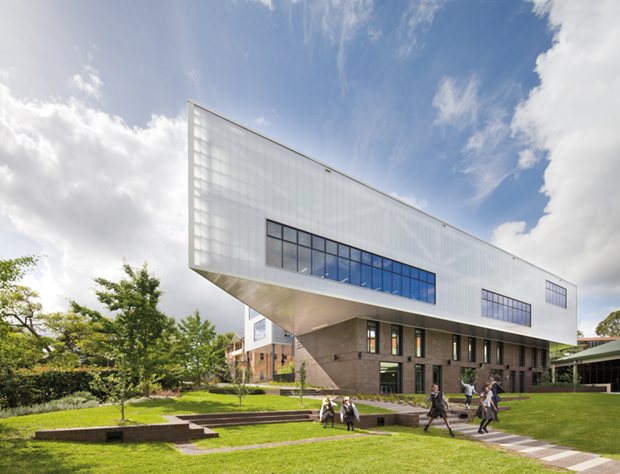
The scheme provides much needed vertical and horizontal connectivity for the school. The proposal unifies both landscape and environmentally sustainable design principals. The facilities allow for best practice and ensure the school’s philosophy of flexibility and an individual approach to teaching and learning.
INITIATIVES
-
Rainwater is harvested and re-used for irrigation of the landscape and flushing of toilets. Energy efficiency is addressed via the use of natural ventilation (mixed-mode), higher than necessary insulation values for the building envelope.
-
The building aims to bring together both passive and active design solutions to sustainability and allow the initiatives to be utilised in the education program for the girls. The building has been designed as a mixed-mode building that is able to operate completely with natural ventilation. Conversely, on extreme weather condition days, the space can be air conditioned. In order to achieve this, the building features a double-skin façade that creates a cavity that in winter is kept closed to retain heat and in summer opens automatically to release heat.
-
The building has implemented the latest environmental technology, there is a double skin façade that creates a cavity that in winter is kept closed to retain heat and in summer opens automatically to release heat. Energy usage will be further minimised by the incorporation of opening windows that are positioned to create cross ventilation with a back up air-conditioning system for the hottest days.
AUSGRID LEARNING CENTRE
Ausgrid Learning Centre submitted by DEM (Aust)
The brief for the learning centre facility was to fulfil Ausgrid’s strategic goal of providing a centre of excellence that would offer a high quality and efficient educational environment for apprentices and teaching staff. It was to consolidate a number of Ausgrid facilities within a world leadership sustainable building, and cater for a variety of training, administration and corporate activities.
The siting and arrangement of buildings was made in response to solar access and prevailing winds.
The building configuration and architectural design were integrated with the mechanical services to minimise thermal loads on the building. Perimeter walkways, external louvres and awnings provide shading and minimise heat gain and glare. On the most exposed northern façade, shading is coupled with high performance glass.
The project is the first in Australia to be awarded both a 6 Star Green Star Education Design v1 certified rating and an As Built v1 certified rating from the Green Building Council of Australia.
INITIATIVES
-
Energy demand management initiatives include:
- a hollow concrete slab cooling system;
- a 260 photo-voltaic (PV) cell system with a maximum output of 51 kW; and
- a gas fired tri-generation plant incorporating a 125 kVA combined heat and power unit and a 95kW absorption chiller used for the air-conditioning system. Heat rejection from the absorption chiller is achieved through the use of 55 geothermal bores beneath the facility which have been drilled up to 100 metres into the earth.
-
Rainwater, harvested and stored in a 150,000 litre capacity tank, is treated and re-used.
-
Grey water is collected, treated and used for toilet flushing and irrigation.
-
Incorporation of biofiltration swales and green roof.
-
Provision of a Building Management and Control System.

-
Achieves high levels of recycled content in reinforcement steel, concrete and timber elements.
-
The sustainable design features have produced a building with approximately 60% less energy usage and 53% less water usage compared to a benchmark building.
-
Teaching and office areas utilise the thermal mass of the building to provide passive cooling. Hollow concrete slabs are used to absorb internal heat gains during the occupied period. The heat is then purged from the slab using cooler outside night air or by mechanical means. Alternatively, the slab is pre-cooled using cooler outside air or mechanical cooling.
-
A gas fired tri-generation plant.
-
55 geothermal heat rejection bores.
-
The Energy Efficiency Centre, incorporating interactive displays, which is open to external visitors.
-
10 electric vehicle charging stations.
-
Paints, carpets, adhesives and sealants were selected carefully to minimise emissions of volatile organic compounds (VOCs).
-
During construction more than 95% of demolition and construction waste generated onsite was recycled or reused. Recycled bricks, timber and steel were used in the building while workstations and equipment were reused from other Ausgrid premises.
-
Approximately 30% of aggregate used within the structure was replaced with recycled concrete or blast furnace slag to reduce the quantity of natural aggregates typically used in concrete.
-
Steel within the structure utilised approximately 70% post-consumer recycled content.
-
Sustainable timber was used extensively, combining Forest Stewardship Council Australia certified timber, and reused and recycled timber.
THE UNIVERSITY OF ADELAIDE INGKARNI WARDLI BUILDING (FORMERLY INNOVA21)
DesignInc Pty Ltd
To satisfy the University of Adelaide’s need for contemporary staff accommodation and Computer Aided Teaching facilities for the ECMS faculty with the high indoor environmental quality criteria established by the Green Star Education Tool. These design imperatives were achieved whilst integrating this modern building within the context of the heritage aspects of the University of Adelaide campus.
Perhaps the biggest challenge to the Sustainable aspects of the project was achieving the 6 star rating under the Greenstar Education tool even after an extensive Value management process when the initial Tender came in over expectation. Another key challenge arose when it became clear that the local Electricity Supply authority would not accept the Buildings tri-generation plant being connected to the Electricity grid. This meant that the system had to be designed so that it operated in “island mode” which added cost & complication to the Building’s Electrical distribution system.
The Building exceeded the normal height restriction applicable to the site, however this was deemed acceptable by the Adelaide City Council as the building was designed sensitively in terms of respecting the adjacent Heritage listed Barr Smith Library building and the overall urban design context of the University campus. Obviously the ESD initiatives within the building went well past the mandatory requirements of Energy efficiency as defined by the Council.
INITIATIVES
-
There is a rainwater harvesting system with 500,000 litre underground storage tanks. This water is used for toilet flushing & irrigation within the building.
-
A gas fired Tri Generation Plant located at the roof level that provides electricity, heating and cooling for the whole building, saving energy use.
-
Lighting throughout the building incorporates Motion sensors so that as people vacate areas of the building in the evening, the lighting will turn off. Because treated air is supplied at low velocity through the floor plenum in combination with the active slab system, the air handling plant is smaller and requires less electricity than conventional air conditioning systems.
-
Key innovative elements include the use of Active Slab technology (hydronic cooling loops within the concrete floor slabs) combined with an UFAD System utilising 100per cent fresh air ventilation, providing a healthy and comfortable internal environment.
-
Heat rejection from the computer server rooms to the ground is achieved via geothermal loops incorporated into the basement diaphragm wall.
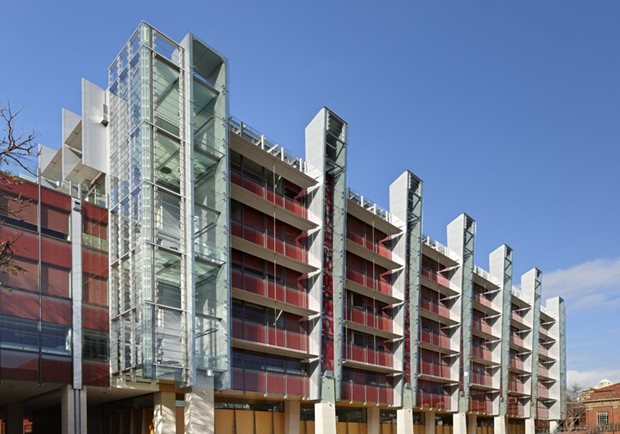
-
The building also has a programmable (DALI) lighting system and a building management system (BMS) designed to reduce energy consumption.
-
The BMS data will be available to students so that the building itself becomes a teaching tool in terms of its Environmentally Sustainable Design.
-
An exhibition space has been incorporated to the south of the building in an area that was previously a car park.
-
This space is roofed with an ETFE (Teflon) inflated roof membrane; another example of innovative material technology in use in this building.
-
Materials selection such as the timber used in the joinery and the carpets throughout was made with careful attention to the origin & method of manufacture of the products with certification required to establish their sustainable claims.
-
Also the furniture and fabrics within the building were selected in relation to their eco preferred content, as well as minimal PVC and formaldehyde content. The sanitary fixtures were chosen for their water efficiency.
-
The site history has been acknowledged with a feature wall in the central void reusing the original Jarrah timber roof timbers recovered from the old mathematics building that was demolished to make way for this building.
-
Paint was selected for its low-VOC content generally.
JEAVONS LANDSCAPE ARCHITECTS
Clifton Hill Rail Project
The duplication of the railway track between Clifton Hill and Westgarth Stations was a key public transport initiative to improve Melbourne’s public transport service, requiring a second rail bridge to be constructed over the Merri Creek (bridgework completed in 2009).
Jeavons Landscape Architects were responsible for implementing a complex landscape architectural brief for the landscape planning and design of green infrastructure along the new track and in the adjoining Merri Creek corridor.
The project required the blending of technically challenging design with aesthetics and high community expectations, including:
Addressing the engineering and operational requirements for the railway and co-ordination with multiple authorities, two local councils, Melbourne Water, and numerous road and rail authorities
INITIATIVES
-
Managing impacts on the Merri Creek corridor including visual impact, recreational trails, natural values, flood flows
-
Restoration of the indigenous creek vegetation and environment, dealing with runoff
-
protection of Aboriginal and non indigenous heritage values (original bridge is heritage listed)
-
Functional and amenity considerations such as pedestrian and cycle routes, design of the interface between the railway and local streets, fully accessible pedestrian crossings over the tracks, viewpoints, safety & sightlines; cycleway signage.
-
Design of a complex intersection on the capital city bike path up a steep slope , advocacy for open space and design of a new small park under the bridge (Bridge Park)
-
Temporary re-routing of cycle networks, and creation of works plans to ensure runoff and the impact of site works were minimised during construction.
-
Merri Creek biodiversity restored

-
The design sought to recreate locally indigenous flora communities of similar species composition and structure to the original ecology.
-
Over 48,000 local indigenous plants were installed after rigorous research.
-
The design approach incises natural vegetation layers with sinuous walls and paths that merge with the organic landforms. A major staircase structure on the south bank cascades down the slope, its basalt sides and angular corten panels evoking the blocky forms, and textures of the basalt cliffs of the valley. The design concept is expressed eloquently in the built form as follows:
-
Restoration of the natural environment with indigenous species and ecological structure based on published research guidelines for the Merri creek valley.
-
The existing heritage listed rail bridge and railway context are reflected and expressed in the landscape through raw materials– corten steel, bluestone slabs and railway ballast gabions.
-
The vegetation composition is tailored to suit each micro-climate from the water’s edge and lower slopes, through the mid-slope, top of slope, cliff-face and grassy woodlands. Our designs are based on the DSE’s ecological vegetation classes, recent research by ARCUE and recommendations of the Merri Creek Management Committee.
-
Bluestone emerged as a significant material, reflecting both natural and social history. As the natural site bedrock and the traditional streetscape material, the sawn, vertical bluestone slabs with broken ends reflect the local basalt cliff-faces provide a contemporary twist and also meet local heritage requirements.
-
Making use of ‘broken’ seconds unusable for Melbourne’s footpaths, these are an especially sustainable, durable material quarried and sawn in Victoria. Basalt also features crushed as railway ballast in the feature gabion walls, and as mulch.
SMART GRID SMART CITY INFORMATION CENTRE
Schreiber Hamilton Architecture
Following being awarded the Federal Government’s Smart Grid – Smart City (SGSC) Project, an initiative to research and gather information about the costs and benefits of smart grids to inform future policy making, Ausgrid was charged with the responsibility of rolling out of new smart technologies across the network to improve the reliability of electrical supply and help reduce the cost of maintaining the network.
A key to this initiative was informing the community of current and future sustainable energy possibilities and initiatives. To enable this in the Hunter Region, Ausgrid partnered with Schreiber Hamilton Architecture, APP Project Management and Hansen Yuncken Builders to bring to life a physical storefront to showcase the future of sustainable energy.
The design objective of the Smart Grid, Smart City Information Centre was to provide a showcase for efficient, sustainable design aimed at "mum and dad" home owners and home buyers, small to medium business owners and community groups. It was to provide public facilities to showcase energy sustainability information, options and products, and to include interactive exhibition displays promoting examples of sustainable energy-efficient technology.
In particular this was to be aimed at the mass-market housing demographic.
The Smart Grid Smart City Information itself is an example of sustainability, and SHA included many examples of recycled and energy efficient materials and technologies into the architecture of the project.
As a showcase project for sustainability, the design called for a higher than normal level of included sustainable technologies, products and features, and this had to be integrated into a modern, consumer friendly, state of the art setting so that customers and visitors could see, hear and feel the message that energy sustainability is affordable, attractive and a viable and available option for energy consumers.
To bring this concept to life as a built environment, SHA and Ausgrid envisaged a centre that acted in harmony with its message and so the Smart Grid Smart City information Centre includes many energy efficient and water efficient materials and technologies, adding an extra level of detail to the sourcing of fittings and fixtures while still keeping to a strict budget.
INITIATIVES
-
Natural light and ventilation opportunities have been maximised to reduce reliance on artificial lighting, minimise energy consumption and take advantage of the temperate climate.
-
The Centre utilises natural light, and is supplemented by a range of low energy lighting options. Lighting products were chosen with energy efficiency in mind and most are connected to control systems which reduce energy use when the Centre is closed.
-
Water-efficient taps and toilets are installed in the bathrooms. The 6 star WELS rated taps use just 4.5 litres per minute. The dual-flush 4 star WELS rated toilets use recycled water, collected from the roof of the building and treated for use in non-potable water tanks in the basement. These toilets use only 4.5 litres for a full flush and 3 litres for a half-flush.
-
An interactive shower display shows users how much water is wasted by inefficient shower heads. The display is served by a high-efficiency water reuse system, including filter and UV light anti-bacterial system.
-
The built form of the project includes individual energy-efficient and water-efficient exhibition display suites throughout the Information Centre.
-
Car parking for the Information Centre, utilises existing tenant basement parking, augmented with electric vehicle charging points for Ausgrid's fleet of MIEV electric cars.
-
Floors: Recycled rubber resilient sheeting, incorporating recycled car tyres and other recycled rubber materials. Bamboo engineered flooring which is highly durable, harvested from sustainable sources, non toxic and includes low VOC adhesives and coatings.
-
Walls: Feature timber wall fabricated from Ausgrid recycled power poles and milled to a custom profile and then “scribbled” across the rear wall of the tenancy.
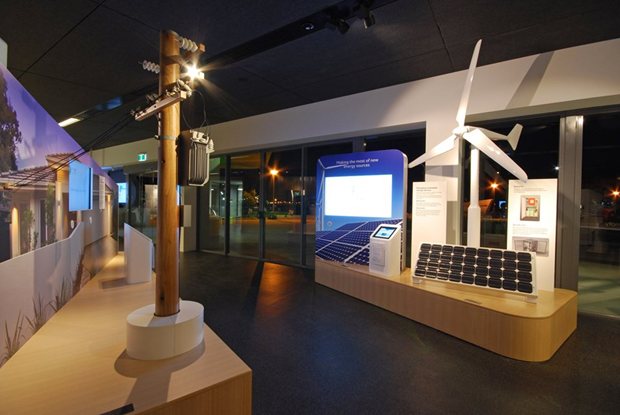
-
Ceilings: Echopanel acoustic panels, produced from recycled and recyclable PET plastic (with approximately 60per cent of PET sourced from post consumer waste materials).
-
Bench tops: Engineered stone with post manufacturing waste materials incorporated as a recycled element.
-
Joinery: Exhibition joinery incorporates X-board Kraft as carcassing, which is a sustainable alternative to MDF, and recyclable at end of life. It is ideal for the relatively short intended design life of the exhibition displays.
-
Demolition and preparation of the tenancy was undertaken in a manner that allows simple reinstatement at the conclusion of the tenancy.
-
While the project was in effect a tenancy fitout only, demolition and preparation was undertaken in a manner that allows simple reinstatement at the conclusion of the tenancy.
-
Daylight mesh stacking chairs are partially constructed from recycled car batteries, which can be recycled at the end of their life.
-
The project includes a very high content of recycled materials, including
-
Feature timber wall fabricated from Ausgrid recycled power poles and milled to a custom profile.
-
Engineered stone bench tops incorporating 42per cent recycled materials recovered from production waste material.
-
Echopanel acoustic panelled ceiling, produced from recycled and recyclable PET plastic (with approximately 60per cent of PET sourced from post consumer waste materials).
-
Recycled rubber resilient floor sheeting, incorporating recycled car tyres and other recycled rubber materials.
-
Bamboo engineered flooring which is highly durable, harvested from sustainable sources, non toxic and includes low VOC adhesives and coatings.
-
Joinery items include X-board Kraft for internal structure, a material which contains recovered paper waste and sugar-cane fibres.
-
In the 60 seat auditorium space, Daylight mesh stacking chairs are partially constructed from recycled car batteries. They can also be recycled at the end of their life.
NOBLE PARK AQUATIC CENTRE
Suters Architects
A key objective was to provide a destination where people from different backgrounds and ethnicities could meet to relax, get fit and socialize all year round. The City of Greater Dandenong is the most culturally diverse municipality in Victoria, with over 56per cent of residents born overseas. Inclusivity was the overarching principal of the design. The Noble Park Swim Centre Consultation Report (July 2009) was commissioned to capture the views of a broad cross section of the community and determine the types of facilities and services required to meet their needs. The outcome was used to inform the final design, with social and cultural interaction a key component.
Some of the challenges were the budget and government funding availability and need to create a facility to last another 50 years or more. Energy and water efficiency, durability, materials and flexibility of space were paramount. Other considerations were the need to maximise reuse of onsite spoil and limiting quantity of imported top soil.
The facility was designed with correct solar orientation in mind. The long building facades face north to south. The east to west short facades windows have been minimised while the north façade takes full advantage of the northern sun. 2m eaves on the north façade limit solar gain in summer and maximise in winter. The building has a mixed mode mechanical system to allow natural ventilation. A series of motorised operable windows and tilt-up panel doors have been provided. The building has been sighted to link-in with the surrounding precinct including sports grounds and community centre and is close to the main road and public transport.
INITIATIVES
-
The facility exceeds Building Code of Australia national requirements.
-
The redevelopment is set to save over 2 million litres of water a year and use 25per cent less energy.
-
A key feature is the reuse of an existing 50m pool shell to store rainwater harvested from the roof. This provides the site and surrounding reserves with 700,000 litres of rainwater storage and reuse.
-
Grey water recycling from showers and basins are utilised for irrigation. Water efficient landscaping has been provided.
-
Gas fired co-generation system providing electricity and heating to the new outdoor 50m pool.
-
Pool filter air scourers to save up to 40per cent of water from backwashing -
-
Water saving fixtures and fittings.
-
Pool covers to conserve water and energy.
-
30 solar roof panels for facility demand and hot water.
-
Mechanical units with heat recovery -
-
Mixed mode mechanical system -
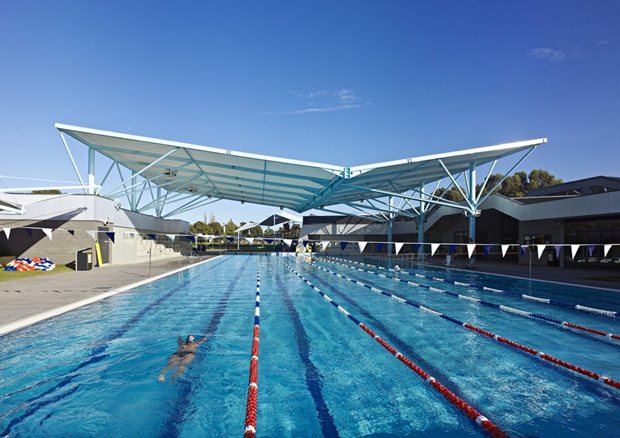
-
Natural ventilation -
-
Light sensors and dimmable fittings -
-
Motorised louvers -
-
High performance double glazing -
-
Walls and roofs insulated and rated above BCA Section J minimums -
-
Natural lighting -
-
2215 sqm of Hydrotect tiles on pool concourse and throughout change rooms and walls (equivalent to planting 70 trees) -
-
Reclaimed timber used on landscape seating. A 42” LCD screen has been installed in the Foyer to display the electricity, gas and water consumption of the building.
-
The screen will also eventually be set up to show a comparison.
Image by Peter Bennetts
SHEARWATER STEINER SCHOOL PERFORMANCE HALL
WD Architects
There is a desire to have a space for the whole school to meet, which is aesthetically beautiful and inspiring, consistent with principles of anthroposophy*, centrally located and accessible to the primary and secondary school, with a quality space for performing and a dedicated, exciting space for indoor sports. Another strong theme coming from the consultation is the desire to create a new and welcoming and naturally beautiful entrance for the school.
Building materials will need to be non-toxic throughout and demonstrate a high level of environmental sustainability, with a preference for local resources as long as it is cost effective to do so.
The clients wanted a unifying facility with ease of access by primary, secondary schools and the public
(outside of school hours).
INITIATIVES
-
Large overhangs due to high rainfall.
-
Cross-ventilation to take advantage of prevailing breezes.
-
Insulation levels to suit the climate.
-
Sunshading optimised for passive-solar design.
-
100per cent energy-efficient lighting.
-
Cross-ventilation for natural ventilation supplemented by ceiling fans; no mechanical systems.
-
Water-efficient plumbing fixtures.
-
Low embodied energy materials where possible.
-
Sustainably-sourced timbers.
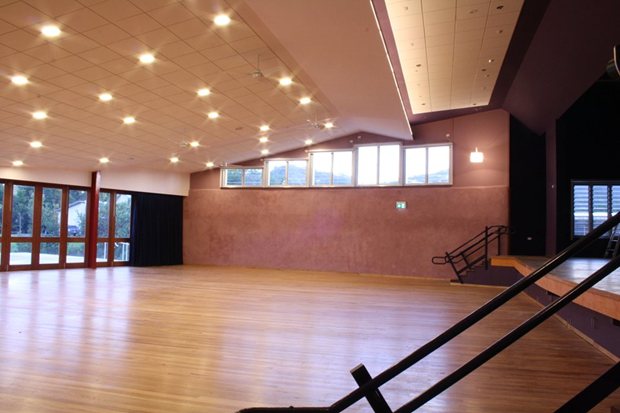
-
Use of extremely low-embodied energy straw bale walls for acoustic and thermal insulation as well as aesthetics and education potential.
-
Livos oil (low VOC, natural) to floors and internal timbers.
-
Resene low- and no-VOC paints throughout; Bauwerk lime paint to straw bale walls.
-
Cypress pine structural timber (see attachment)
-
Sustainably-sourced Eco-certified joinery timbers
-
CHH Shadowclad plywood claddings.
-
lifecycle impact of design and specification was considered and
-
addressed. Sunshading modelling was undertaken as well as review of lighting
-
design to energy-efficiency.
FLINDERS MEDICAL CENTRE
Woodhead Pty Ltd
The brief, based on earlier masterplanning studies, identified a range of functional issues to be addressed. The major issues were focussed on deficiencies with the L3 ‘hot’ floor which included Operating theatres, Emergency Department and Intensive Care.
A collaborative procurement strategy was engaged that saw the client, the design team and the constructor working together to prioritise and deliver a redeveloped Health Facility that addressed all the client objectives.
Woodhead’s review of the endorsed masterplan at concept stage resulted in an alternative option which addressed buildability/access/budget and Decanting issues. This new direction resulted in a new Womens Health building not in the original scope. The new 4 storey wing enabled greater flexibility to decant from areas critical for hot floor expansion and enabled greater continuity of existing services.
Delivering excellence in Environmentally Sustainable Design was defined as a key result area for the $163M Redevelopment, and the New South Wing at FMC is the first Green Star Healthcare Design v1 certification in Australia.
The redevelopment has also served as a catalyst for the introduction of a new model of care throughout the hospital. This required that ‘standard’ solutions were replaced with a highly consultative user group engagement in designing responsive physical facilities that reflect the new patient focussed health delivery model.
INITIATIVES
-
The new components of the redevelopment have been designed to maximise daylighting and views whilst incorporating passive design elements to reduce heat gains.
-
Installation of a displacement ventilation system- a first in South Australian hospital context. It allowed generous provision of natural ventilation to the patient rooms: This system was incorporated into the customised bed head joinery allowing minimal impact on the space.
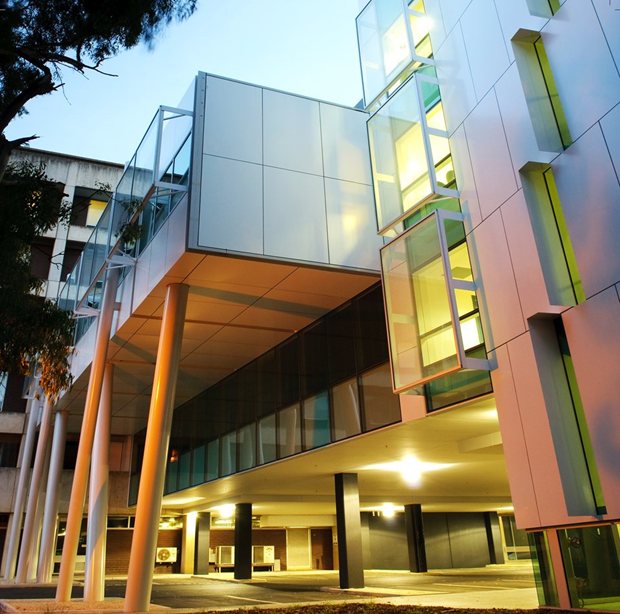
-
A sustainable Procurement Guide developed through the NSW project is now utilised on other SA Health projects. This guide provides valuable ESD benchmarks for the complex procurement process.
-
Validation of materials selections let to the education of suppliers and manufacturers, of products specific to Healthcare markets, regarding the additional ESD/ Greenstar criteria.
-
Contractually at least 80per cent of waste by weight (from demolition and construction) was required to be reused or recycled.