Just as the concept of sustainability has evolved over the years, so has the idea of environmental leadership. The sense of accountability across the architecture and design community has matured significantly; thoughtful ESG strategies are on the rise, decarbonisation efforts guide business strategies across the industry and the era of transparency has bid farewell to the years of greenwashing.
Unquestionable experts in facade and ceiling solutions, Network Architectural always strived to prioritise sustainable solutions as part of their trajectory, with their unnerving pursuit of transparency, compliance, quality and commitment considered second to none. And now, through their partnership with PanelCycle, Network Architectural enables customers to take the sustainable option where recladding is concerned.
“We first partnered with PanelCycle about two years ago,” says Llewellyn Regler, National Technical Manager at Network Architectural. “At that point in time, it was known that you could recycle aluminium composite panels, but no one had anything set up in that space. They were the first independent company to do so, and partnering with them made great sense”.
PanelCycle provides a full solution to recycle combustible Aluminium Composite Panel cladding removed from Australian buildings. Their process diverts 100% of the materials from landfill, and uses those materials for manufacturing right here in Australia. The PanelCycle process covers four steps:
Step 1: Transport. As part of this initial stage, PanelCycle provides tailored transport solutions for each site with their extensive background within the construction industry.
Step 2: Recycle. Then, upon removing the cladding from a building, the organisation recycles combustible ACP cladding, diverting 100% of it from landfill.
Step 3: Processing. ACP cladding is broken down through a specialised machine, and separated into aluminium and core material.
Step 4: Consumption. The separated materials are then utilised to manufacture new products that are fed back into the construction industry.
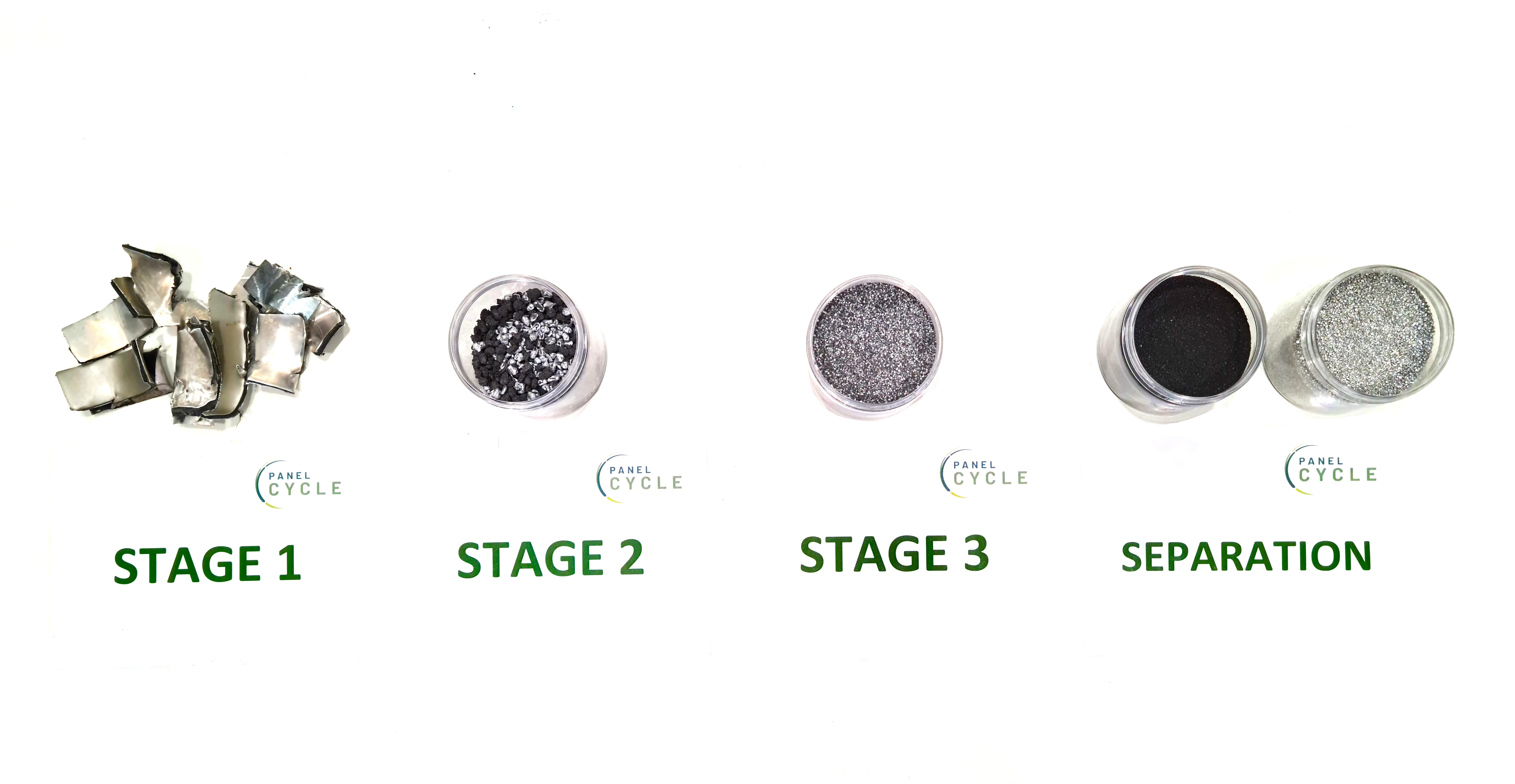
“We offer the service as an add-on to our clients,” says Llewellyn. “Or we point them directly to contact PanelCycle. For us, the important thing is that the panels are being recycled.” He notes that things have come a long way since even just a few years ago when aluminium composite panel waste was treated essentially the same as asbestos.
Instead, through PanelCycle, there is now a traceable chain of custody for the waste. “PanelCycle will collect the panels from site, acknowledge that they’ve taken receipt, then provide detailed independently audited reporting after processing to prove how they’ve been processed and where they’ve gone,” says Llewellyn. He explains that PanelCycle will source documentation from the aluminium recycler and from the location the core materials are recycled at. “You actually have a lifecycle view of where those panels have ended up, which is really important,” Llewellyn says.
Llewellyn notes that across the industry, people are very receptive to recycling the panels as part of the broader push towards more sustainable lifecycle management of construction materials. Particularly, as recycling the panels is also more cost-efficient. “The cost to recycle is actually less than the cost of putting the panels into landfill,” he sums up. “And by recycling you know you’re part of the solution – not part of the problem.”